With supply chains accounting for the bulk of most organizations’ greenhouse gas (GHG) emissions, ports will play an important role in meeting future emissions reduction targets. Ports are fast-paced environments that require enough power to support fleets of vehicles, cranes, container handlers and more, continuously moving heavy loads with minimal downtime. Terminals are considering technologies like lithium-ion batteries and hydrogen fuel cells to replace tried-and-true internal combustion engines (ICE) in order to help meet these targets. The question then becomes, how should these operations evaluate the emerging electrification options?
Factors like performance, cost and reliability are critical. Unlike ICE power, which depends on well-established fossil fuel supplies, ports looking to electrify operations must pay attention to local electrical infrastructure and hydrogen fuel supply.
The Limitations of Full Reliance on Lithium-ion
In warehouse and manufacturing environments, there is a long history of using battery power to operate smaller equipment like forklift trucks. How does this approach stack up to the realities of powering large container handling equipment at ports?
Battery-powered electric vehicles rely heavily on the electrical grid. That same grid brings electricity to homes and businesses, with the average household using less than 30 kWh per day. Charging a single container handler with a 500 kWh battery pack uses significantly more energy. A fleet of 20 such vehicles charged daily could use more than 20,000 kWh every day. And the power required is enough demand to overload grid capacity.
Meanwhile, ports use almost every square inch of space to maximize storage capacity, accommodate cranes and provide pathways for container handling equipment. Battery charging stations can be bulky, so finding the right place for them within a terminal layout is key, especially for larger fleets requiring more space, more power and a consistent charging schedule. Ideally, an operation would locate several charging stations throughout the port, near employee break areas, to allow for easy charging during breaks.
It can take anywhere from 90 minutes to six hours to fully recharge a battery for a large container handler, depending on the charging setup. A fully-charged battery typically lasts between four to eight hours. Due to the necessity of frequent recharging and the hours required to fully recharge, equipment spends significant time out of service. For operations accustomed to ICE power with run times that last the equivalent of several eight-hour shifts, a switch to battery electric power could require purchasing more units to maintain the same level of equipment availability.
Terminals are considering technologies like lithium-ion batteries and hydrogen fuel cells to replace tried-and-true internal combustion engines (ICE) in order to help meet future emissions reduction targets.Courtesy of Hyster.
Hydrogen Fuel Cells as an Alternative Power Source
Ports seeking another alternative for their heavy-duty fleets should look at hydrogen fuel cells, which possess key differences compared to lithium-ion battery power. While these trucks will still have (smaller) lithium-ion batteries, they are not relying on the battery for energy storage. For one, fuel cells do not need to be recharged. Instead, operators refuel a tank of hydrogen; in terms of duration, this process is closer to ICE refueling than lengthy battery recharging. Yet while diesel-powered vehicles produce tailpipe GHG emissions during operation, equipment powered by hydrogen fuel cells emit only water and heat as byproducts.
Additionally, powering equipment with hydrogen generally requires less infrastructure and space than relying solely on battery power, due in part to the time necessary to refuel and the associated run time. For large equipment with big tanks, it can take as little as 15 minutes to fill an empty tank sufficiently to provide eight to 10 hours of continuous run time. In other words, hydrogen-powered units do not need to refuel as frequently as batteries need to be recharged, nor do they spend nearly as much time parked at refueling stations.
Crucially, hydrogen fuel cells work in tandem with an onboard lithium-ion battery. The fuel cell can power equipment directly or charge the onboard lithium-ion battery, which itself can also power equipment and capture regenerative energy from braking and load lowering.
Considerations in Sourcing Hydrogen Fuel
Hydrogen can be generated on site or delivered to storage and fueling stations. The amount of hydrogen an operation needs is a critical factor in determining what method of hydrogen sourcing to use. For a single truck, a bundle of hydrogen tanks is sufficient, but when consumption hits 200 kg per day, delivery by tube trailer is more appropriate. When consumption passes 800 kg per day, on-site generation starts to make the most sense. An operation’s location can also dictate the economics of delivering hydrogen to a facility, as on-site generation becomes increasingly attractive with greater delivery distance.
Finally, note that neither hydrogen nor electricity are primary fuels, so understanding the complete carbon impact requires looking at the feed stocks from which they are produced. Two emerging types of hydrogen production processes are thermochemical and electrochemical. Thermochemical processes use natural gas, coal or biomass to extract hydrogen molecules. Meanwhile, electrochemical processes use electricity to split water into hydrogen and oxygen. Currently, 4% of hydrogen energy worldwide is produced through a wide variety of alternative sources, but the primary source is a thermochemical process called steam methane reforming (SMR), which, it should be noted, also produces GHGs.
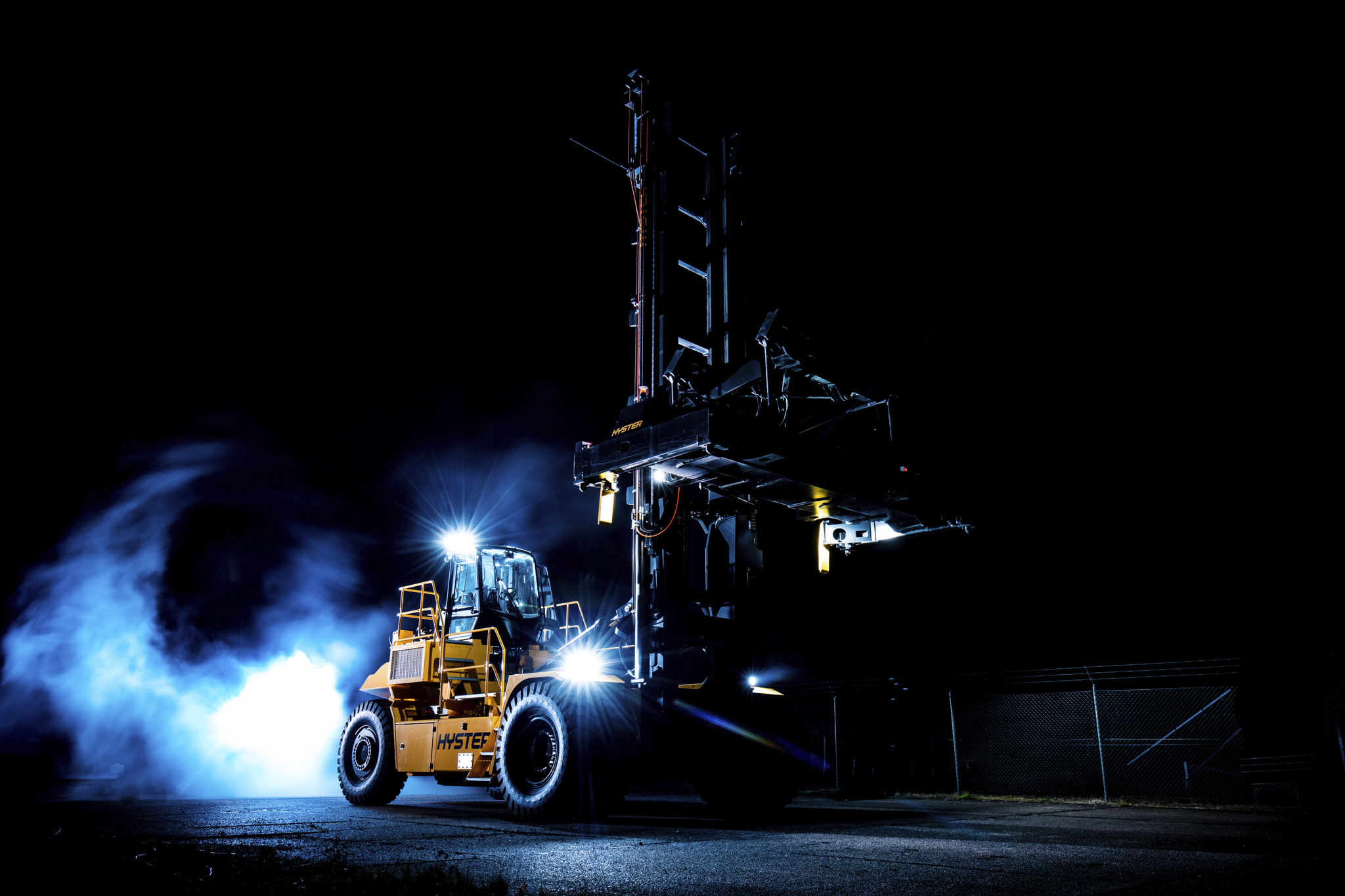
Recognizing the Full Potential of Hydrogen at Ports
Potential applications for hydrogen in port settings go beyond upgrading fleets of reach stackers and container handlers. Hydrogen fuel cells can also power the terminal tractors that ports use to transport shipping containers inside the yard.
Hyster Company recently began testing of a top-pick container handler powered by hydrogen fuel cells at Fenix Marine Services (FMS) at the Port of Los Angeles. A California Climate Investments grant awarded by the California Air Resources Board in 2018 helped support development of the HFC-powered container handler. Elsewhere in the world, Hyster is engaged in a pilot of a fuel-cell powered Reach Stacker at the Port of Valencia, a fuel cell-powered empty container handler at a terminal in Hamburg, Germany and has partnered with Capacity Trucks to develop electric and hydrogen powered terminal tractors.
The development of hydrogen infrastructure and hydrogen fuel cell-powered equipment is happening now. Real-world deployments of port equipment powered by hydrogen fuel cells are underway, and large companies are also joining forces to build regional hydrogen networks to produce and distribute hydrogen fuel at scale.
As ports consider how best to electrify, it’s important to consult with an expert to understand whether hydrogen is the right long-term fit.